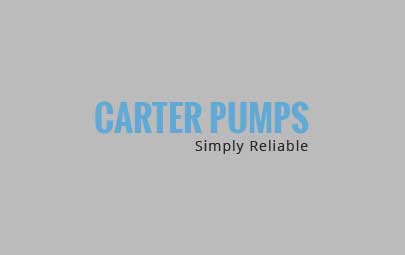
Grease pumps with waste traps are commonly used for a variety of applications, including pumping commercial waste trap grease. The grease will be pumped from one location to another that is suitable for treatment. One of the most popular pumps for this task is the diaphragm pump, which is commonly found in restaurants, hospitals, correctional facilities, or other government installations where grease must be transported for treatment.
How This Process Works
Typically, an engineer will be assigned to create a pump unit which can be used for large mixing in a building that has multiple areas, such as a shopping mall with restaurants. The grease must be transported from the grease pit to the location where it will be collected. The challenge that the engineer will face is correctly configuring the piping in such a manner where it is compatible with both the building’s structure and the local laws regarding waste grease management. Prior to the implementation of the pump system, the owner of the building would contact and collaborate with an engineering firm which could assist them in developing an efficient pumping mechanism.
Correctly Positioning The Pump
Positioning the pump correctly is extremely important. For this task tools such as Solid Works or CAD will frequently be used. The engineering team will collaborate with the building contractor to determine the location of pumps within the parking space. Since most shopping malls are designed for an upscale consumer experience, the pumps will usually be surrounded by a fence in an area that is sequestered away from public viewing. Ideally, the pumps should largely be unnoticed by most shoppers.
In addition to correctly positioning the pump, it is also important to choose the right model. The best grease pumps are those which are simple to use, and which require little maintenance. The diaphragm is subject to wear, but should be affordable to replace and easy to change.
Panels, Switches, Training And Installation
These pumps come with a control system that is integrated and which will feature a panel. They have a function which is on/off automatically, as well as an indicator which is float level and which can detect when grease pits should be emptied. The pumps will activate whenever the grease pit fills up and will deactivate when they become empty, which provides both energy savings as well as greater operational efficiency.
The control panel features sensors which will notify maintenance crews when over pressurization is present, resulting from blockages either in the line or a valve that is closed. An alarm will start which will result in the pumps shutting themselves down so that damage to the equipment is avoided. Many diaphragm pumps have positive displacement, which means they should not operate against valves which are closed.
When the pumps are ready to be installed, a representative from the firm will visit the site to provide training and instruction to the maintenance crews. This crew will typically be responsible for a primary pump as well as a backup which will be used in the event of pump servicing or failure. This allows for consistent operation that is disruption free.