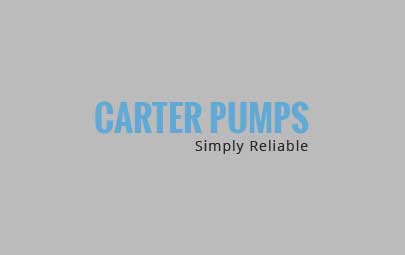
Plunger pumps do fail, and it is not uncommon for that to happen. But it doesn’t mean you need to immediately go out and buy a new pump. With the right expertise and know-how, the plunger pump can be fixed, especially if the failure is due to one of the common plunger pump problems. Typically, these problems are:
Pump Motor Fails To Start
There are many reasons why this could happen. Some of the reasons include motor damage, low line current, blown fuse, open circuit in limit switches and timers, or open thermal overload.
Pump Runs But Fails To Deliver
If the motor is running but the pump is still not doing its job, this could be because the valve has been incorrectly installed. Also check if the valves are worn or dirty, if there is insufficient hydraulic oil, if the suction or discharge line is blocked, or the pump is not primed.
Pump Delivers At Low Capacity
Check the same issues as the above. Aside from that, the liquid viscosity may be too high, there could be a leak, starved suction or excessive suction lift, incorrect capacity setting, or the liquid is close to boiling point.
Pump Delivers Too Much Capacity
This could be due to excessive suction pressure, or insufficient discharge pressure.
Pump Operates Erratically
There may be blockage in the suction piping, always use a strainer in the suction line to catch debris from entering a pump during installation. Also, ensure the size of the pipe is not smaller than the suction connection.
Noisy Pump
Possible reasons are improper lubrication, excessive gear wear, and in particular worn bearings.
Motor Overheating
The hydraulic oil may be too viscous, there is improper wiring, low voltage, or high ambient temperature. Do also check the pressure rating of the motor operating the pump discharge.
Oil Leakage
Check the diaphragm head bolts are tightened, the oil cap is secured, or the breather cap if it is not loose. Also check if the pump is overfilled with oil.
Discharge Pipe Issues
Ensure the size of the discharge pipe is suitable for the application, and has the right pressure rating in excess of the pump’s design.
Issues With Auxiliary Equipment
Similar to the pump and pipes, any auxiliary equipment also needs to be of the right size. This includes back pressure and safety relief valves, pulsation dampeners, calibration cylinders and controls.
Old Seals Become Unreliable
If the seal designs are old, usually engineers or operators will not have confidence that they are reliable and can last a decent length of time. This is something that must certainly be checked before commencing operations.
Improper Placement Of Pump
The location of the pump in your building may also cause trouble, as extreme fluctuations in temperature can affect pump performance.
If you have any issues with your pump, don’t hesitate to speak to Carter Pump, the leader in plunger pumps since 1897. With our credibility and expertise, we would certainly be able to diagnose the problem for you, and solve it in a jiffy, most likely without you having to replace the pump at all. Contact us for more information about our services!