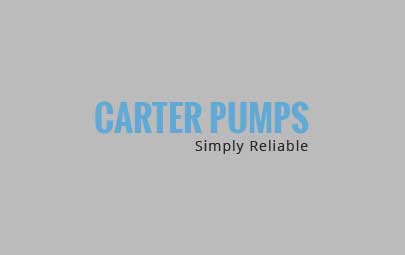
In many industrial applications and machinery, there are pneumatic cylinders used. They are also sometimes known as pneumatic actuators or air cylinders. Working with such industrial machines, it is important to know about pneumatic cylinders, so that you can understand how they work, especially if they break down and there is a need to fix or replace them.
What Is A Pneumatic Cylinder?
A pneumatic cylinder is a type of actuator, which is a device that translates a source of static power into useful output motion, for example, to apply a force. Actuators typically are mechanical devices that convert energy into motion, such as blocking, clamping or ejecting.
Pneumatic cylinders are mechanical devices that use compressed air acting on a piston inside a cylinder to move a load on a linear path. Unlike the hydraulic alternatives, the operating fluid in a pneumatic cylinder is simply air, so there is no risk of leakage and contamination of the surrounding machinery components as compared to the hydraulic cylinders.
There are many styles of pneumatic actuators. Some of the varieties include diaphragm cylinders, rodless cylinders, telescoping cylinders, and through-rod cylinders.
How A Pneumatic Cylinder Works
The most popular type of pneumatic cylinder is made up of a piston and rod, moving within a closed cylinder. There are two subcategories of this cylinder based on how they operate, namely, single acting and double acting.
Single-acting cylinders use one airport which allows compressed air to enter the cylinder, moving the piston to the desired position. A spring is used to return the piston to its original position once air pressure is removed. Double-acting cylinders, on the other hand, have an airport at each end to move the piston back and forth using alternating blasts of pressured air.
Typically within an application, the actuator body is connected to a support frame and the end of the rod is connected to a machine element that is to be moved. An on-off control valve directs compressed air into the port to be extended, while opening the port to be retracted to the atmosphere, creating a pressure difference within the cylinder which, if the load connected to the rod is less than the force created by the force of the pressure differential multiplied by the surface area of the piston, will move the load. The machine element position can be reversed by reversing the compressed airflow.
Pneumatic cylinders help to power other components, but they are rarely seen, unlike other components such as compressors, filters, pressure regulators, lubricators, on-off control valves, and flow controls. All of these components are connected together by a network of piping or tubing (either rigid or flexible), and fittings. It is crucial to take into account the pressure and flow requirements of the cylinders or actuators in an application system when selecting these other components, to ensure the desired performance.
How To Fix A Broken Pneumatic Cylinder
If your pneumatic cylinder has failed, it could be tricky to try to replace it yourself. Your best bet is to consult a professional such as Carter Pump, which offers complete technical support and repair services and would be able to advise you on your best course of action. Contact Carter Pump today for your repair needs!